CASE STUDY
999 Boundary Road
$55,000
REBATES
RECEIVED
246,168 kWh
ENERGY
REDUCTION
$41,000
ANNUAL
ENERGY COST SAVINGS YEARLY
$55,000
REBATES
RECEIVED
246,168 kWh
ENERGY
REDUCTION
$41,000
ANNUAL
ENERGY COST SAVINGS YEARLY
ABOUT THE COMPANY
As one of Canada’s premier industrial real estate providers, Pure Industrial delivers full-service solutions in logistics hubs essential to the national supply chain. Their facility at 999 Boundary Road is a state-of-the-art distribution center spanning 20 acres, equipped with 47 truck-level doors, one grade-level door, and clear heights from 22 to 25.3 feet.
ABOUT THE COMPANY
As one of Canada’s premier industrial real estate providers, Pure Industrial delivers full-service solutions in logistics hubs essential to the national supply chain. Their facility at 999 Boundary Road is a state-of-the-art distribution center spanning 20 acres, equipped with 47 truck-level doors, one grade-level door, and clear heights from 22 to 25.3 feet.
THE CHALLENGE
THE CHALLENGE
The facility was originally equipped with 330 high-output T5 fluorescent high bay fixtures, each operating with six 54-watt lamps, resulting in a total power consumption of 360 watts per fixture. Over time, this outdated lighting system led to several operational challenges. Illumination throughout the space was inadequate and uneven, with noticeable dark spots and shadowing that affected visibility. The lighting also suffered from poor color rendering, making it difficult to accurately perceive colors in the work environment. Additionally, the system's high energy consumption resulted in an annual usage of 658,252 kilowatt-hours, significantly increasing operating costs. These issues raised concerns about both safety and efficiency, while the frequent need for maintenance and lamp replacements further contributed to rising operational expenses.
THE CLIENT NEEDED TO INCREASE THE LIGHT LEVELS TO PREVENT POOR LIGHT DISTRIBUTION AND DARK SPOTS.
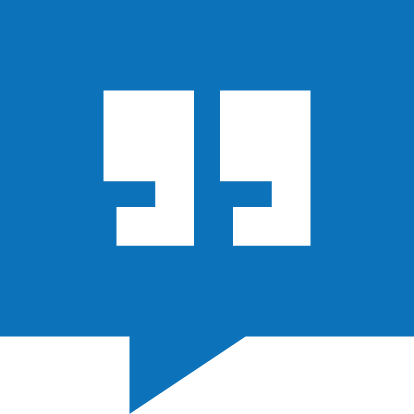
The facility was originally equipped with 330 high-output T5 fluorescent high bay fixtures, each operating with six 54-watt lamps, resulting in a total power consumption of 360 watts per fixture. Over time, this outdated lighting system led to several operational challenges. Illumination throughout the space was inadequate and uneven, with noticeable dark spots and shadowing that affected visibility. The lighting also suffered from poor color rendering, making it difficult to accurately perceive colors in the work environment. Additionally, the system's high energy consumption resulted in an annual usage of 658,252 kilowatt-hours, significantly increasing operating costs. These issues raised concerns about both safety and efficiency, while the frequent need for maintenance and lamp replacements further contributed to rising operational expenses.
THE CLIENT NEEDED TO INCREASE THE LIGHT LEVELS TO PREVENT POOR LIGHT DISTRIBUTION AND DARK SPOTS.
THE SOLUTION
THE SOLUTION
The customer and their client selected the following RENO Lighting products as the ideal replacements.
BACK-LIT PANEL
The AIM Series (20/25/30/35W) Back-lit Panel was chosen to replace the 111 x 4 lamp T8 32 W fluorescent fixtures at 114W each.
LINEAR HIGHBAYS
The ZENITH Series (180/210/230W) Linear Highbay was chosen as the replacement for the 330 fluorescent fixtures.
The customer and their client selected the following RENO Lighting products as the ideal replacements.
BACK-LIT PANEL
The AIM Series (20/25/30/35W) Back-lit Panel was chosen to replace the 111 x 4 lamp T8 32 W fluorescent fixtures at 114W each.
LINEAR HIGHBAYS
The ZENITH Series (180/210/230W) Linear Highbay was chosen as the replacement for the 330 fluorescent fixtures.
THE RESULTS
THE RESULTS
Following a comprehensive lighting assessment, our team recommended the Reno R35302 back-lit flat panel troffer as an energy-efficient, high-performance replacement for the outdated fluorescent system. All legacy fixtures were replaced with the R35302 panels, resulting in a significant transformation throughout the facility.
The new lighting system delivered increased light levels and a notable reduction in energy consumption. Maintenance costs also decreased due to the long lifespan and reliability of the LED panels, reducing the need for frequent replacements and servicing. Most importantly, the office environment saw a remarkable improvement in visual comfort and overall workplace productivity.
With uniform, evenly distributed illumination across all areas, the previous issues of dark spots and inconsistent lighting were fully resolved—creating a brighter, safer, and more efficient workspace. This upgrade not only improved day-to-day operations but also contributed to long-term cost savings and sustainability goals.
Following a comprehensive lighting assessment, our team recommended the Reno R35302 back-lit flat panel troffer as an energy-efficient, high-performance replacement for the outdated fluorescent system. All legacy fixtures were replaced with the R35302 panels, resulting in a significant transformation throughout the facility.
The new lighting system delivered increased light levels and a notable reduction in energy consumption. Maintenance costs also decreased due to the long lifespan and reliability of the LED panels, reducing the need for frequent replacements and servicing. Most importantly, the office environment saw a remarkable improvement in visual comfort and overall workplace productivity.
With uniform, evenly distributed illumination across all areas, the previous issues of dark spots and inconsistent lighting were fully resolved—creating a brighter, safer, and more efficient workspace. This upgrade not only improved day-to-day operations but also contributed to long-term cost savings and sustainability goals.